Your cart is currently empty!
Your paper printer can print multiple pages.
Why shouldn’t your 3D printer?
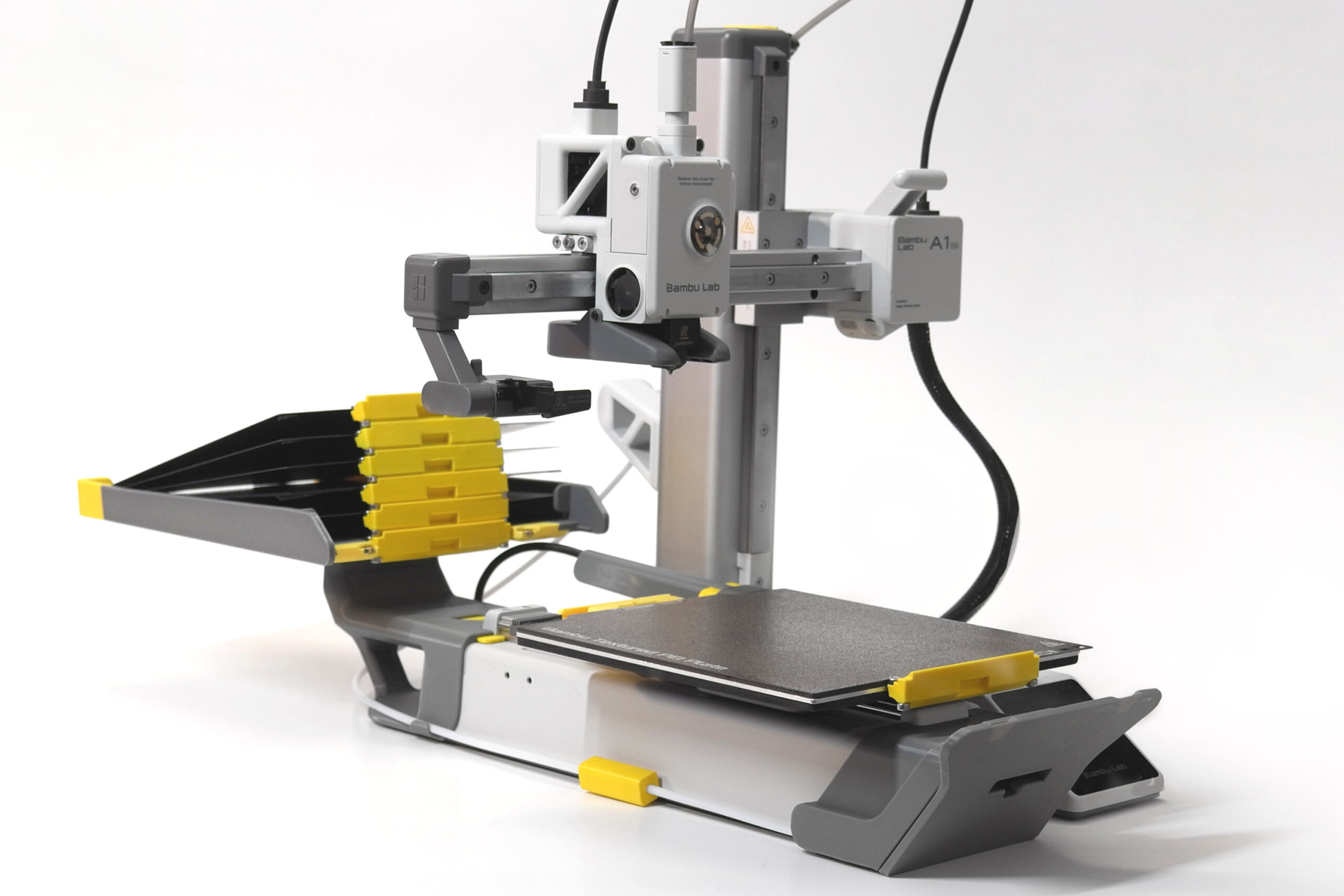
Introducing swapmod
Swapmod is an easy-to-install add-on for a BambuLab A1 Mini that enables it to print multiple plates in sequence, fully automatically.
Why you need
swapmod?
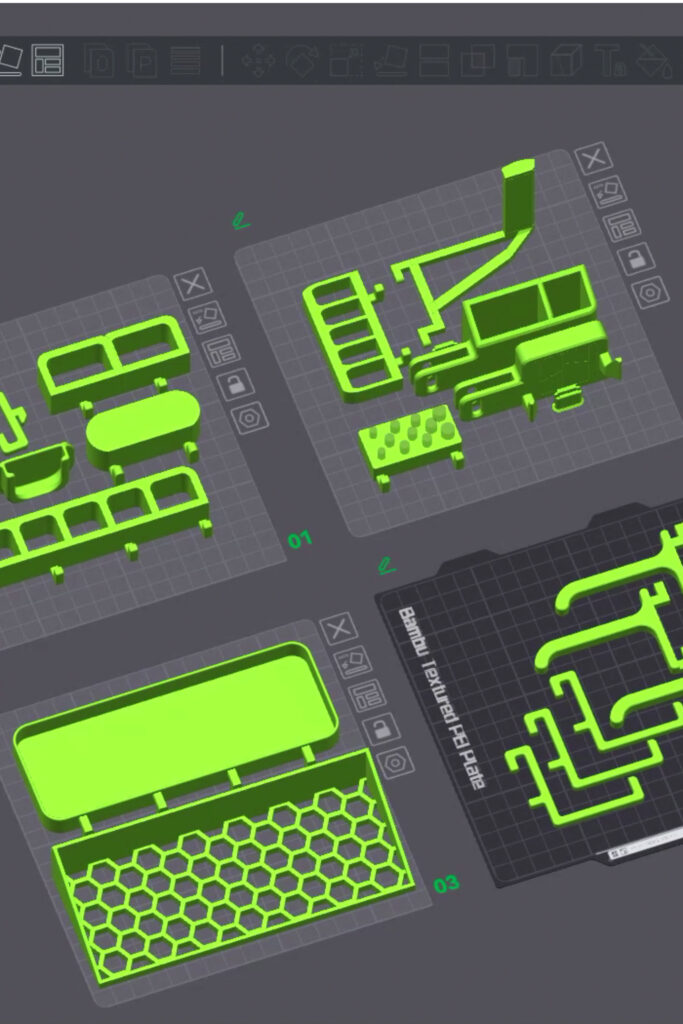
Think big
No matter your printer’s size, print multi-part projects and entire product batches with ease. Stop cramming all your parts onto one plate to avoid or minimize restarts. With swapmod your BambuLab A1 mini scales up to a “maxi” and produce all needed parts in one go, limited only by the size of your largest piece. For example, nine plates in the magazine create an effective print area equal to 54cm x 54cm. Plus, ejected plates can be reloaded mid-print, giving you even greater flexibility.
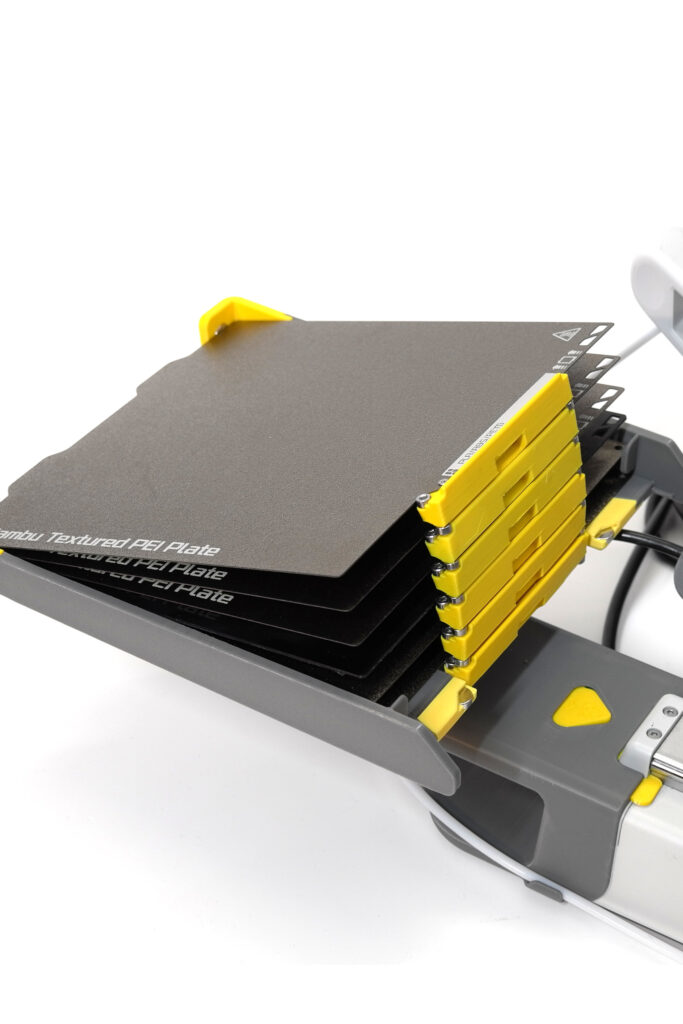
Gain more comfort
With swapmod, youโll still need to collect your finished parts from the printer, but now you can do it on your schedule, not the printerโs. No more late-night restarts to meet production deadlines. Your swapmoded printer takes care of it for you.
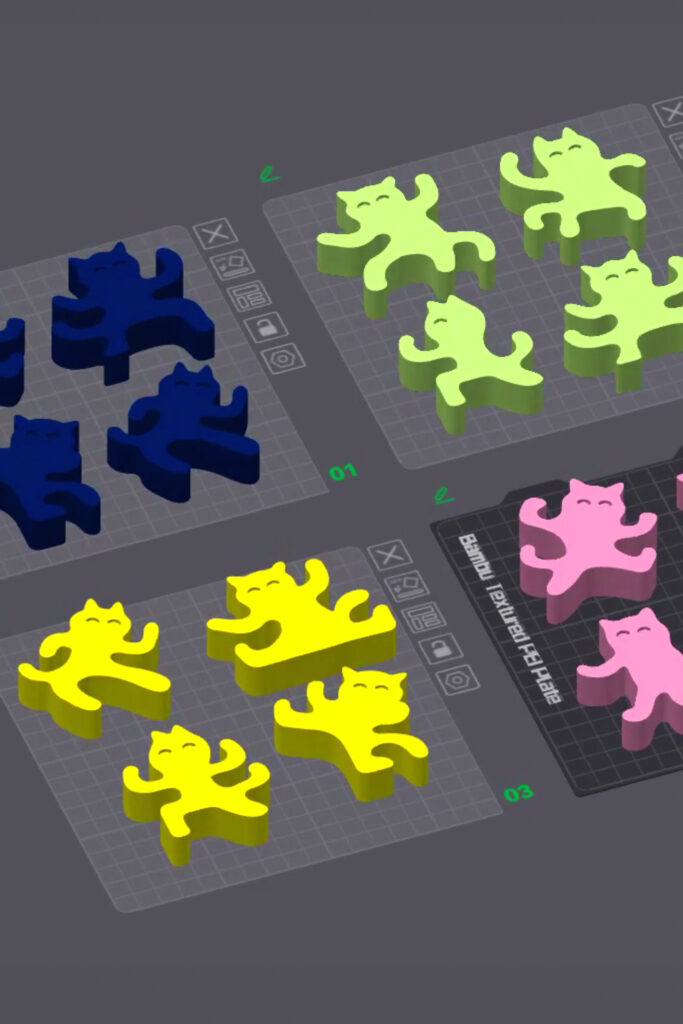
Print efficiently
Printing objects of different colors on one plate wastes material and takes excessively long due to frequent material swaps. Swapmod minimizes this when printing one material per plate.
Model: “Ninja Cats Stacking Balance Game” by Valeria Momo & Mattia / Source: Makerworld
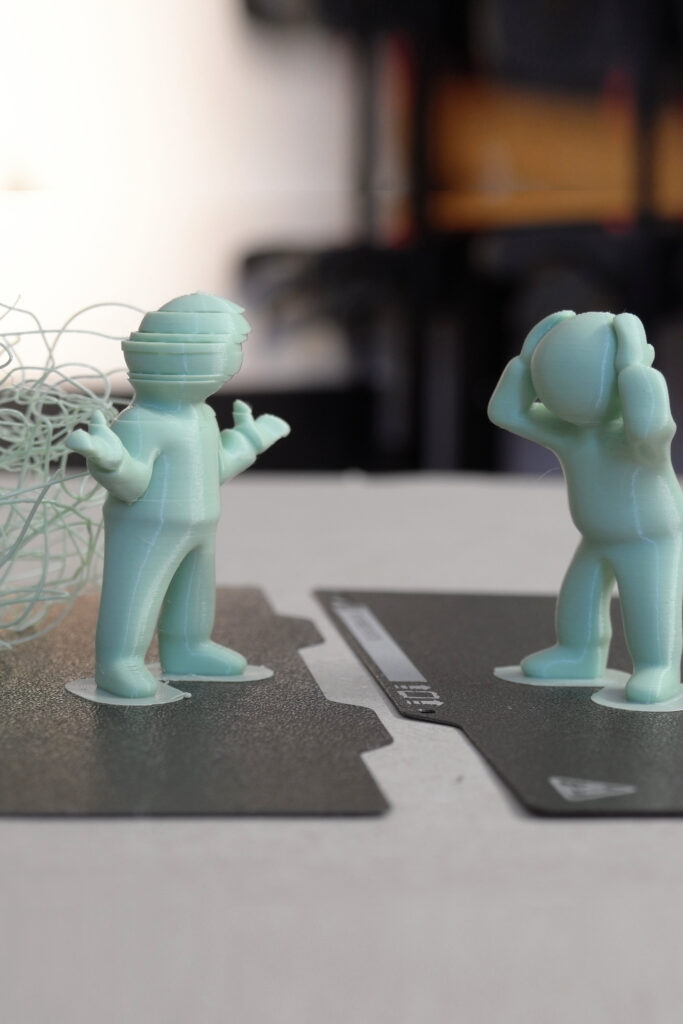
Produce reliable
Weโve all seen one failed part ruin the rest. With swapmod you can distribute parts across multiple plates to minimize this risk. If one plate fails, the others stay intact. Itโs perfect for โtroublemakerโ parts or those needing delicate finishes or special printing techniques like vase mode.
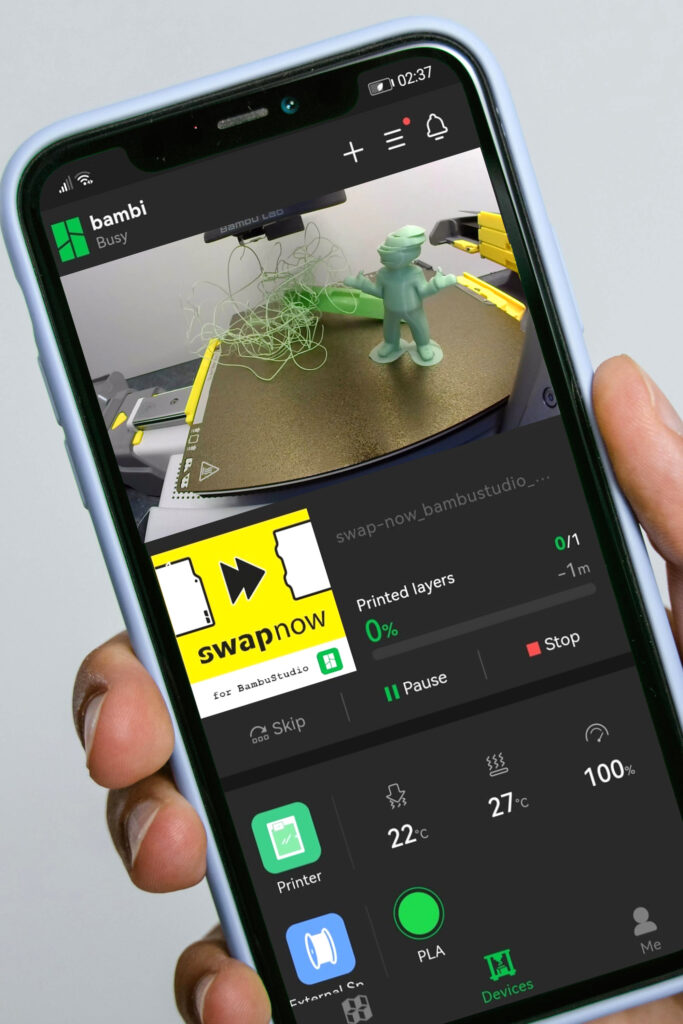
Control remotely
Swapmod enables true remote control of your printer using existing connectivity. Now you can remotely replace the build plate and restart printing from your slicer or HandyApp using a โswapnowโ file. This file doesnโt contain any printing data but just tells the printer to eject the current plate and load a new one, letting you โreloadโ your printer from virtually anywhere.
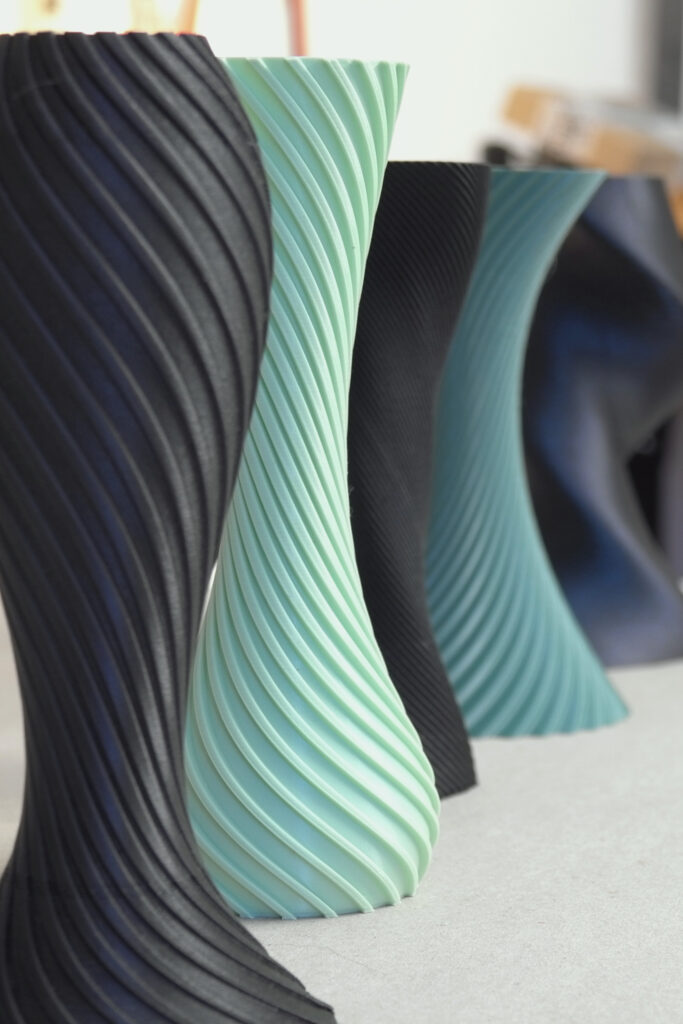
Scale your business
Start or scale your business with minimal investment and reach more customers. Labor is a major factor in 3D printing and often a bottleneck, as someone must be there to clear the build plate and start the next print when finished. This makes scaling and scheduling difficult. Swapmod solves this by automating restarts, allowing plate clearing and part collection at your convenience without machine downtime. This also makes your calculation easier. When your part takes 3 hours you can easily calculate how many parts you can produce in a day/week/month because you don’t have to deal with downtime factors which makes this calculation so tricky.
You still
have
questions ?
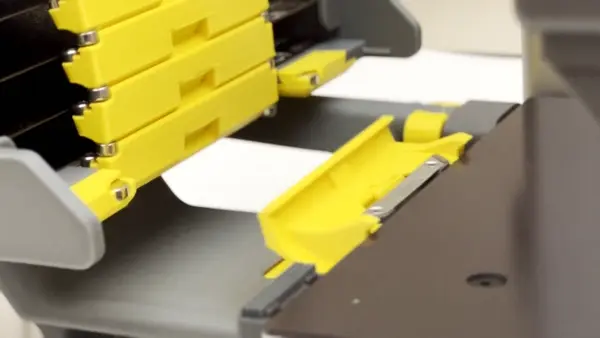
How does it work?
After starting the print queue, your printer will load a blank plate from the magazine, print on it and when complete, simply eject the finished plate and replace it with the blank one loaded from the magazine. This process is repeated until all the plates in the queue are printed or the magazine runs out of plates.
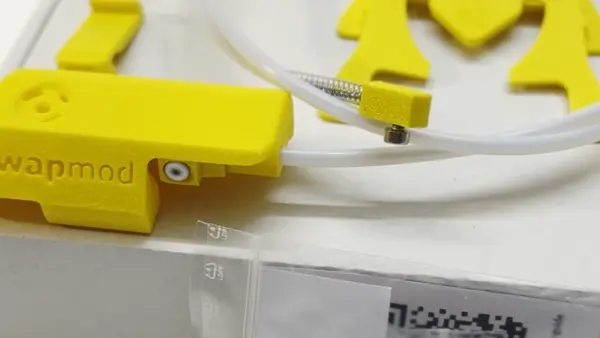
Can I build it?
The kit has been designed with ease of use in mind, so that almost all of the parts can be simply clicked into place like building blocks. All the steps are shown in a detailed video tutorial. As there are no complex mechanics, wiring or other electronics involved, it’s also a nice little project to build together with your kids.
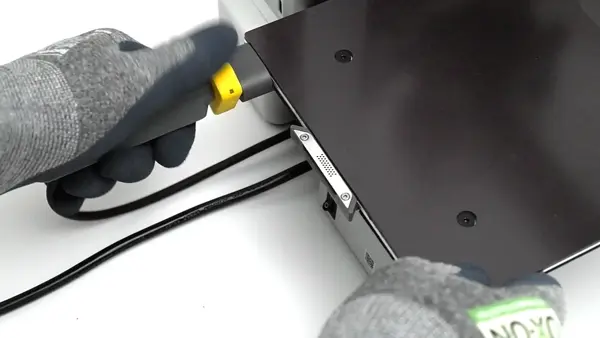
How to install?
Attaching (and releasing) the swapmod parts to (and from) your printer can be done with the ease of a snap. Almost all parts are snap-fitted using metal springs and spring bars. A self-test file will help you check that everything is working properly before you start printing.
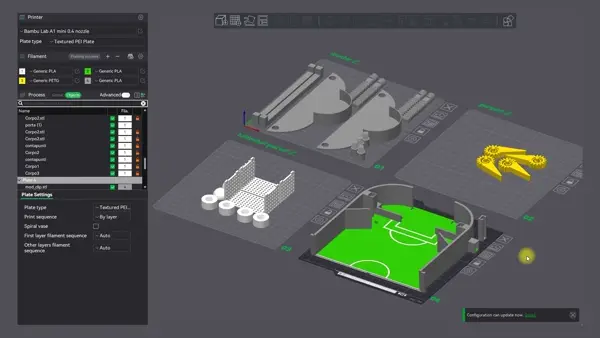
How about software?
To operate with swapmod, you will continue to use your usual slicer (BambuStudio and OrcaSlicer) with the difference that before you press the “print” button in the upper right corner, you will have to carry out an extra step. Since BambuStudio and OrcaSlicer do not (yet) support multi-plate printing, there will be an application that emulates this functionality.
This application runs in any browser such as Firefox, Chrome or Safari and is available for online and offline use. There is no installation or subscription required. The application only acts as a converter, creating a queue before starting to print, so it doesn’t need to run during printing. It can also be used to change the order in which plates are printed, the number of repeats and to combine multiple files into a single queue.
Update 2025.01.25: In mid-January, BambuLab announced their plans for security and connectivity changes in the upcoming firmware. We have been following BambuLab’s blog posts and are eagerly awaiting further developments. As of today, we have no indication that the announced changes will affect the functionality of swapmod. The application used with swapmod converts the files and does not connect to the printer, cloud or slicer. The only scenario where it could stop working is if BambuLab decided to close their sliced files by signing them with a key. We have not seen any information about their intention to do this.
Why
on earth
is it a kit?
- Cost. First of all, it’s the price. Designing it as a kit is an opportunity to save a lot of money for both the manufacturer and the customer. It makes no sense to sell printing- and assembly time to a maker who owns a 3D printer. It’s like selling bread to a baker, isn’t it?
- Availability. In the same amount of time it takes to produce one fully printed add-on with all the parts, a printer could produce five kits. Offering a kit makes it possible to manufacture on a large scale without building a huge print farm or using expensive third party suppliers (who probably don’t use automation).
- Quality & sustainability. We all know that the bigger the printed part, the more likely it is that something will go wrong during printing. If the user prints a functional part and it’s not perfect, but it works, it’s likely to be used anyway. If the manufacturer has some aesthetic flaws in its parts, they need to be thrown away or at least recycled (which I plan to do). Otherwise, the risk of receiving a complaint or even finding pictures of that particular part somewhere on social media or review sites is quite high. This is the other side of the “quality control” coin. Reducing the number of parts produced by the manufacturer automatically reduces a lot of avoidable waste.
- Logistics. Shipping large parts usually means shipping a lot of air, packaging and cushioning material. All this adds to the price and is not sustainable. It’s much better if most of the product is made locally, because shipping a bag of granules or a spool of filament is always more sustainable than shipping printed parts (unless you’re printing solid cubes).
- Vision. I liked the idea of BambuLab’s hardware kits right from the start. Most of them are “just” toys for now, but the idea is visionary. It’s a first big step towards the next generation of products. I truly believe that in the not too distant future, a 3D printer will be a part of most households, just like a microwave or a fridge.